IMPACT
Shipping is currently responsible for around 1.1 billion metric tons of CO2 emissions (around three percent of global total). Replacing fossil oil with regenerative marine fuels can save more than a gigaton of CO2 every year. For container ships, green methanol is currently gaining traction as a climate-neutral fuel alternative.
Today's production of methanol is based on a century-old and emission-intensive manufacturing process based on fossil gas or coal. C1 Green Chemicals, in collaboration with CreativeQuantum and Leibniz Institute for Catalysis (LIKAT), has developed a new, highly efficient catalyst that revolutionizes this process. This enables the cost-efficient production of green methanol from non-fossil feedstocks such as biomass or CO2. The process will facilitate a methanol economy in which the utilized carbon is used in a continuous cycle instead of generating additional CO2 emissions.
The goal of the project is the scalable production of market-ready green methanol for marine and aviation applications.
Technology
For the market rollout of the e-methanol process, individual process steps - and in particular their coupling into a process chain - need to be optimized. The goal of the project is to realize the overall process of electricity-based synthesis gas generation and a radically re-developed methanol synthesis process under real conditions for the first time worldwide.
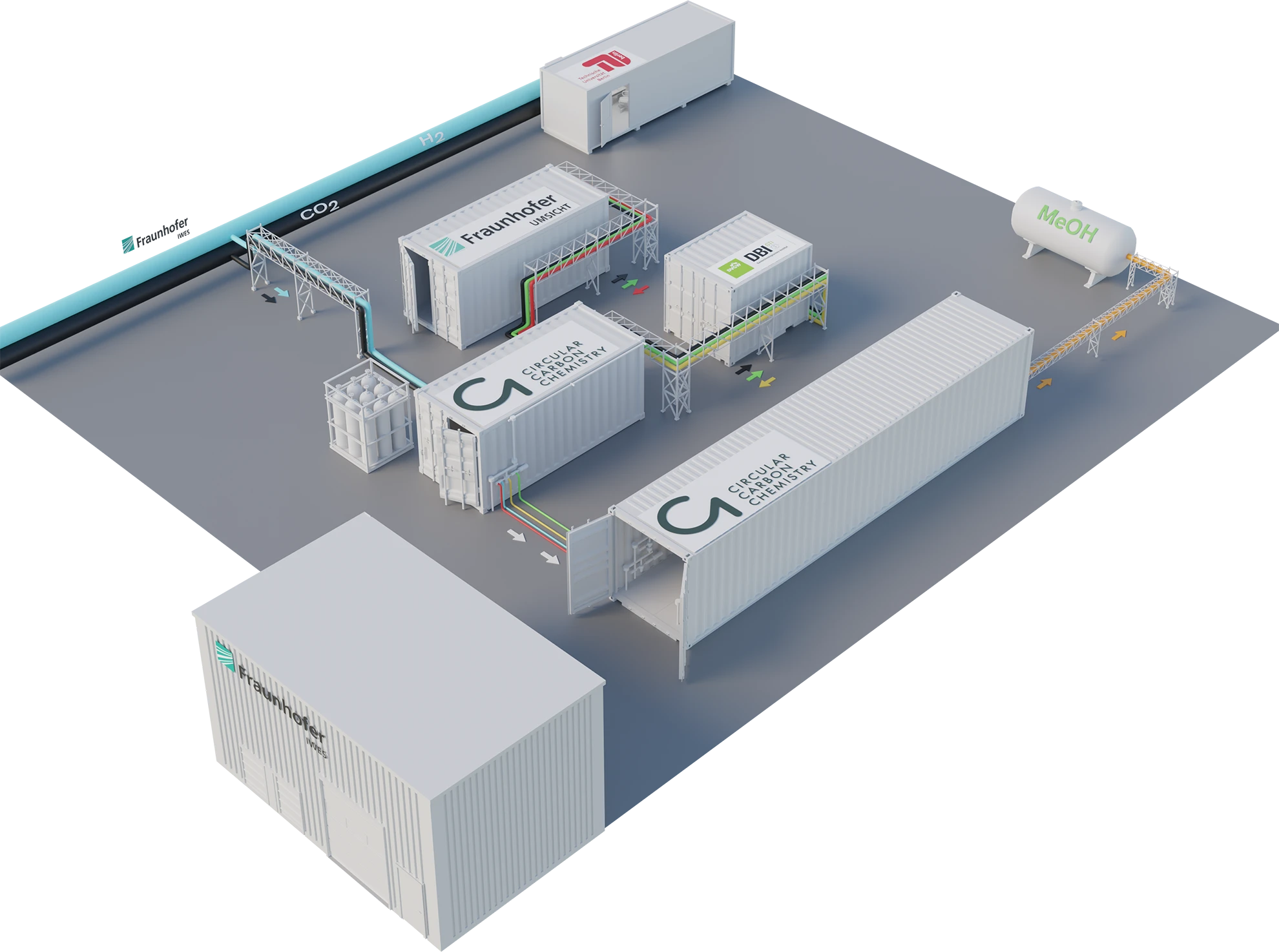
C1 Green Chemicals provides the new catalyst as well as the reactor for the homogeneous catalysis of methanol, which was developed in-house and realized with the company OilRoq from Halle (Saale). This will be paired with two different technologies for the CO2-based generation of synthesis gas as feedstock: Fraunhofer UMSICHT is supplying a new low-temperature co-electrolysis, DBI-Gastechnologisches Institut gGmbH Freiberg is using an industrial reverse water gas shift unit. Fraunhofer IWES provides the on-site location and infrastructure at Hydrogen Lab Leuna and evaluates the load flexibility of the components and the overall process. The Technical University of Berlin is developing an efficient operating concept based on a dynamic overall process model and is creating application-oriented mathematical methods for evaluating and optimizing load-flexibility.
In addition to the potential of electricity-based and load-flexible use of synthesis gas generation, a central innovation is homogeneous catalysis for methanol generation itself. For the first time in the world, not a two-dimensional surface reaction with solid catalysts (heterogeneous catalysis), but a three-dimensional, scalable reaction in the liquid phase (homogeneous catalysis) is used, invented by C1 Green Chemicals in collaboration with CreativeQuantum and Leibniz Institute for Catalysis (LIKAT). Not only is this highly selective, more scalable and suitable for load-flexible operation, it also offers cost advantages regardless of plant size.
The CO2 used originates from industrial process emissions. With the integrated end-to-end process chain, "Leuna100" creates the prerequisite for RED II-compliant production of green methanol. The final evaluation of the methanol produced for its suitability as marine fuel and for further processing into kerosene ensures its applicability.
Funding
The “Leuna100” project starts in August 2023 in the Leuna Chemical Park and will run for three years. It is funded with a total of € 10.4 million by the German Federal Ministry for Digital and Transport as part of the Funding Programme Renewable Fuels. The funding guideline for the development of renewable fuels is coordinated by NOW GmbH and supported by the project management agencies VDI/VDE Innovation + Technik GmbH and Fachagentur Nachwachsende Rohstoffe e. V.
Consortium
C1
Green Chemicals AG
C1 develops new, climate-friendly chemical production processes by rethinking chemical reactions from the atomic level all the way up to the production scale. The chemical processes are designed with the help of quantum chemical simulations and implemented in proprietary production technologies. In doing so, the Berlin-based company develops and scales exclusively on the basis of renewable raw materials and energy. From the first steps in the development of a production process, all processes are designed to enable a closed carbon cycle. In this way, C1 supports industry on its way to net-zero.
More informationDBI-Gastechnologisches
Institut gGmbH Freiberg
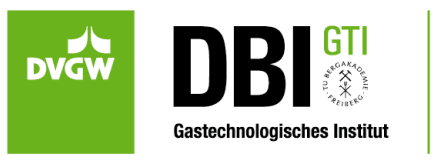
DBI-Gastechnologisches Institut gGmbH Freiberg is a non-profit institution active in the field of application-oriented R&D. The status of an affiliated institute of the TU Bergakademie Freiberg results in considerable synergies. Especially in the field of transfer of process engineering from laboratory to pilot plant scale, DBI is leading in several projects. Here, it can draw on a large number of successfully completed and ongoing R&D projects and a broad spectrum of staff expertise, including in engineering (planning project engineering, P&ID flowsheet generation, electrical planning, process safety, automation). This is supported by R&D expertise in the field of synthesis gas generation, with DBI having several test rigs available for investigating reaction engineering processes as well as corresponding analysis technology.
More informationFraunhofer
UMSICHT
Fraunhofer UMSICHT is pioneering the way to a sustainable world. With our research in theareas of climate-neutral energy systems, resource-efficient processes and circular products, we make concrete contributions to achieving the 17 Sustainable Development Goals (SDGs) of the United Nations. We develop innovative, industrially feasible technologies, products and services for the circular economy and bring them to application. The focus is on the balance of economically successful, socially equitable and sustainable developments.
More informationFraunhofer
IWES
Fraunhofer IWES secures investments in technological developments through validation, shortens innovation cycles, accelerates certification procedures, and increases planning accuracy by means of innovative measurement methods in the wind energy and hydrogen technology sectors. At present, there are more than 300 scientists and employees as well as more than 100 students employed at the nine sites: Bochum, Bremen, Bremerhaven, Görlitz, Hamburg, Hanover, Leer, Leuna and Oldenburg.
More informationTU Berlin
The Department of Dynamics and Operation of Technical Plants at TUB is intensively involved in modeling, simulation and optimization for the design and operation of diverse processes in process engineering. Here, economic efficiency, energy efficiencyand sustainability are in the focus of the research work. In addition to systems process engineering, fundamental research in the field of fluid dynamics and separation efficiency, as encountered in thermal separation processes, represents a further core competence. At the department, manifold efforts are made in the field of intensified processes. For example, novel concepts for homogeneous catalysis in innovative switchable solvent systems (microemulsions) as well as novel reactor and operating concepts for heterogeneous catalysis are brought to process maturity.
Research partner
Leibniz Institute for Catalysis,
Team Prof. Matthias Beller
The Leibniz Institute for Catalysis e.V. (LIKAT Rostock) has over 70 years of "know-how" in the development of high-performance catalysts. Originally dedicated exclusively to catalysis, the institute is now one of the largest publicly funded research facilities in the field of applied catalysis in Europe. The methodological and materials expertise of the more than 300 employees focuses on the development of resource-saving processes.
More information